Call us: +1 315 791 4196 | Email: info@trayotek.com
FDM (Fused Deposition Modeling)
Imagine a hot glue gun that builds things up instead of melting them down. That’s kind of like FDM 3D printing! FDM, which also goes by the cooler name FFF (Fused Filament Fabrication), is a way to make 3D objects layer by layer, like building a tiny brick castle.
Here’s how it works: The printer uses a special kind of plastic like you might find in toys or water bottles. This plastic comes in thin spools of thread called filament. The printer heats up the filament, melting it into gooey goodness. Then, it squirts this melted plastic out of a tiny nozzle, following a computer plan layer by layer. As each layer cools and hardens, another gets added on top, and before you know it, you’ve got a 3D-printed object!
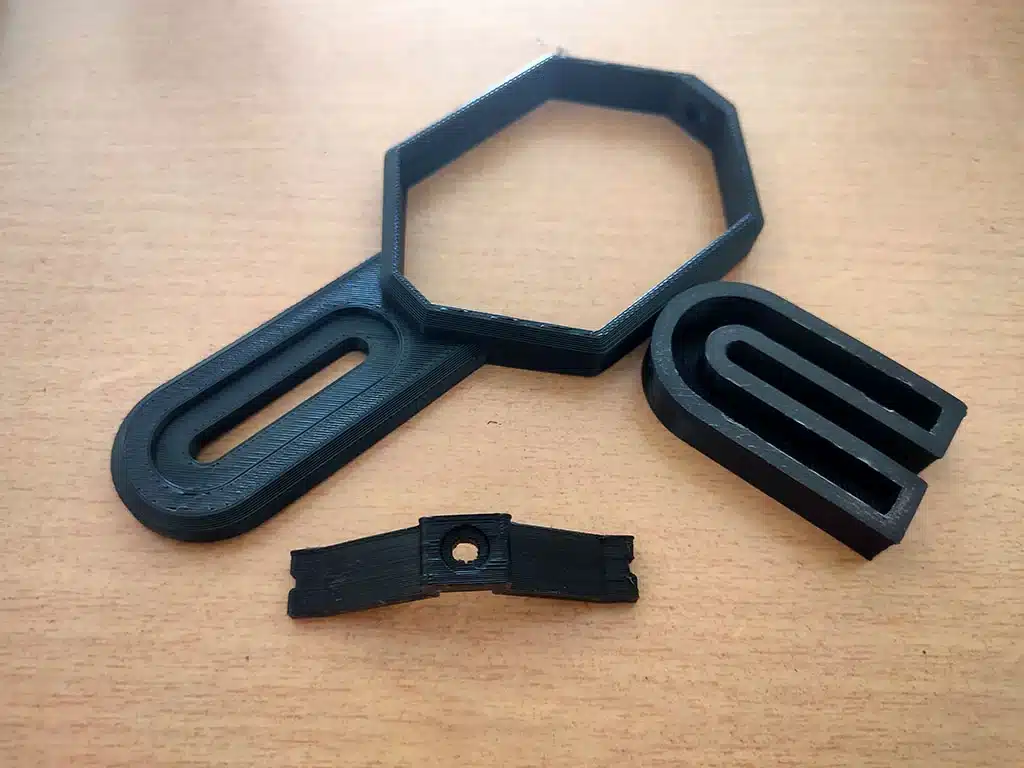

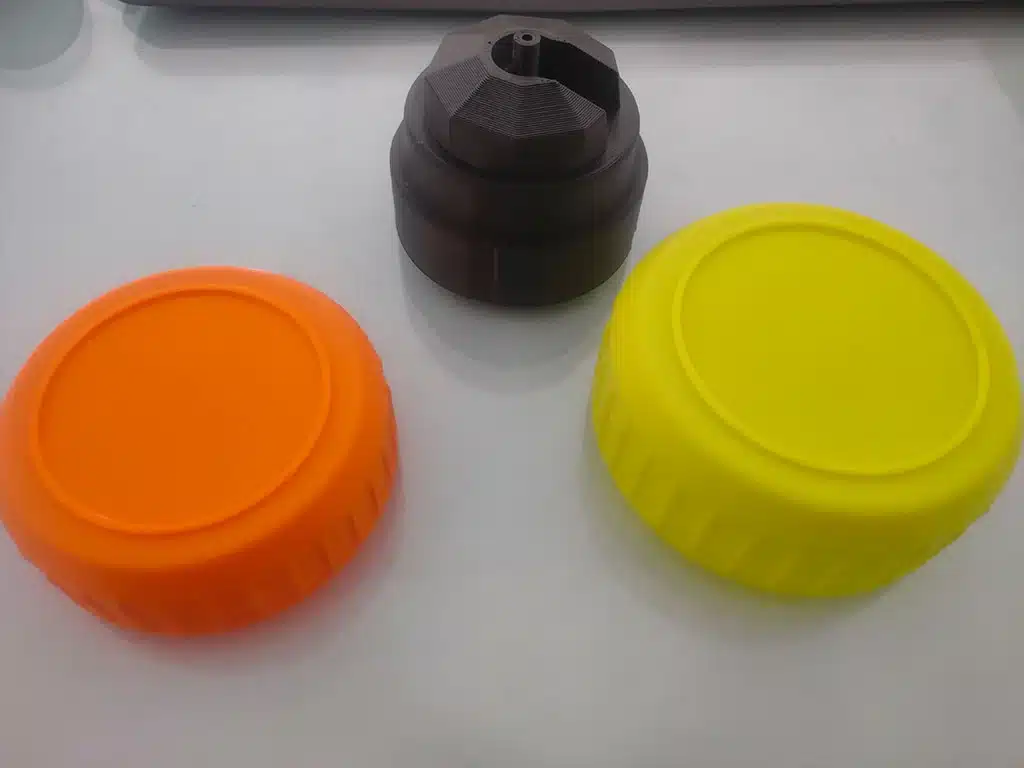
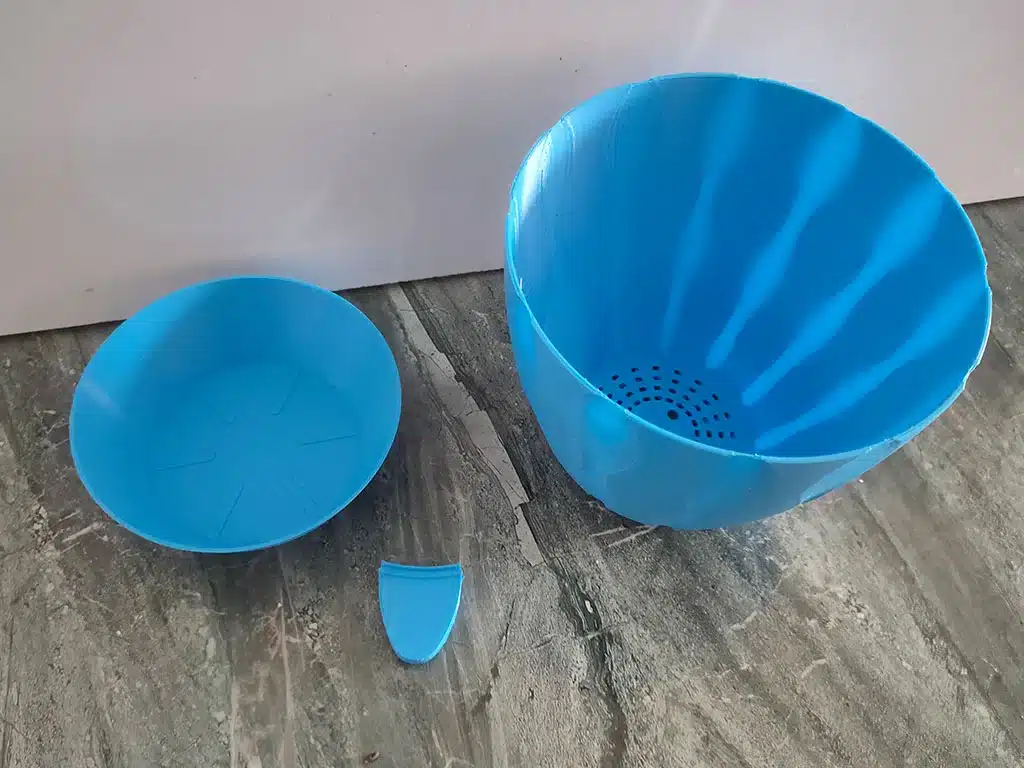

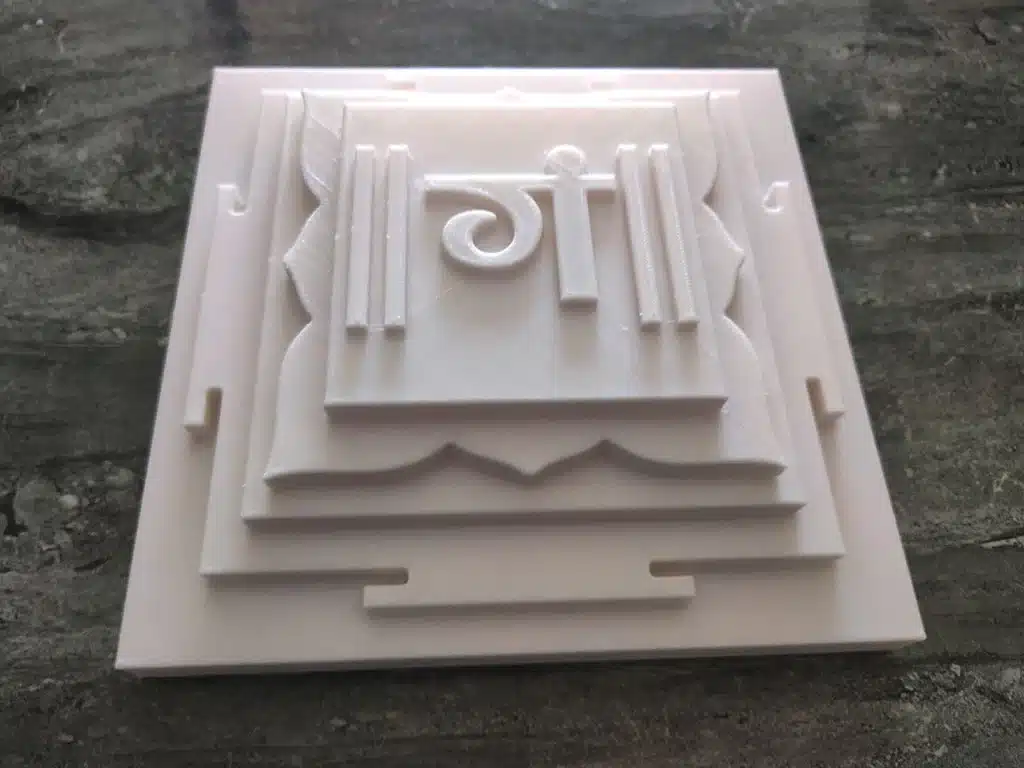



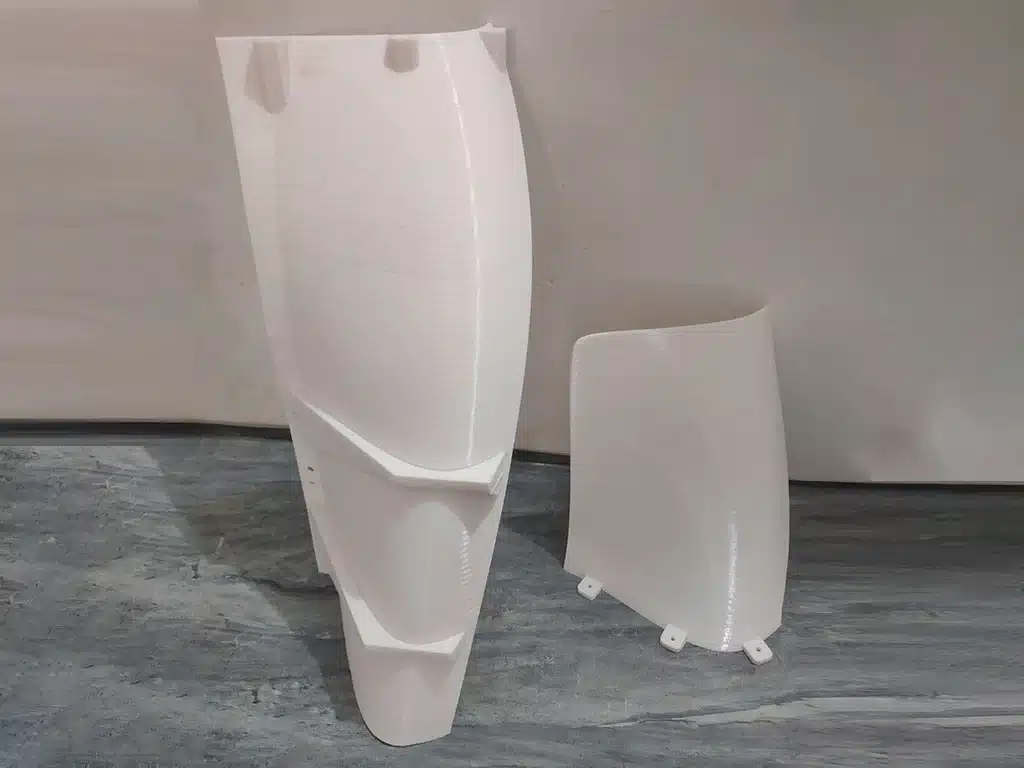
FDM (Fused Deposition Modeling) 3D Printing Services
FDM uses CAD design files that are uploaded to the machine itself and translates them into physical dimensions. Material for FDM includes polymers such as ABS, PLA, PETG, PC, etc… which the machine feeds as threads through a heated nozzle.
FDM is the most common, recognizable, and widely available 3D printing technology. FDM printers can build parts quickly and with a lot of strength in a range of thermoplastics at an economical cost.
FDM is a filament-based technology that works by melting thermoplastic via a heated extruder. The melted plastic is then deposited onto the printer’s build platform one layer upon another layer. Each layer hardens and cools down instantly upon the previous layer, binding both layers together. Support structures are created where needed or for more complex overhanging geometries.
Technical requirements For FDM
- Minimum Wall thickness: 2 mm
- Minimum details size: 2 mm (for text/ hole diameters etc)
- Layer thickness: 0.1 mm – 0.3 mm
- Max dimensions: 550 x 550 x 550 mm. Large parts can be created by assembling individual parts by interlocking designs or gluing them together.
- Standard Accuracy: ± 0.3% (with a lower limit of ± 0.3 mm).
- Lead Time: Minimum 2 working days for despatch (It depends on Part)
- Surface finish: visible layers with texture
FDM 3D Printing Applications
- Prototypes for form, fit, and function testing
- Prototypes directly constructed in production materials like PLA, ABS, Nylon
- Low-volume production of complex end-use parts
- Patterns for Sand casting & molds with lesser detailing
Suitable Materials for FDM
- PLA (Polylactic Acid) is a biodegradable thermoplastic derived from renewable resources such as corn starch or sugarcane. It is used for low-cost, non-functional prototyping. Offers greater detail than ABS, but is more brittle. Unsuitable for high-temperature applications. Comes in a range of colors, properties, and finish options such as silk, glow-in-the-dark, and color change in temperature.
- PLA – Carbon Fibre
- ABS (Acrylonitrile Butadiene Styrene) has good mechanical properties, with excellent impact strength, superior to PLA, but less defined details. Commonly used for enclosure prototypes.
- ABS – Carbon Fibre
- PetG (Polyethylene Terephthalate Glycol) is a thermoplastic material with improved mechanical properties over PLA and excellent chemical and moisture resistance.
- PetG – Carbon Fibre is the ideal filament for anyone that desires a structural component with high modulus, excellent surface quality, dimensional stability, lightweight, and ease of printing.